Jaw crushr operate manual: how to install, repair and examine it
2022-09-30
Davis - staurk machinery
In this article , we will mainly talk about 3 aspects of jaw crusher , as below: Guide line :
1.How to install the jaw crusher?
2.how to opreate the jaw crusher?
3.how to repair and examine the jaw crusher?
Related: jaw crusher introduction , parameter,working princeple
Download: jaw crusher operation manual.pdf
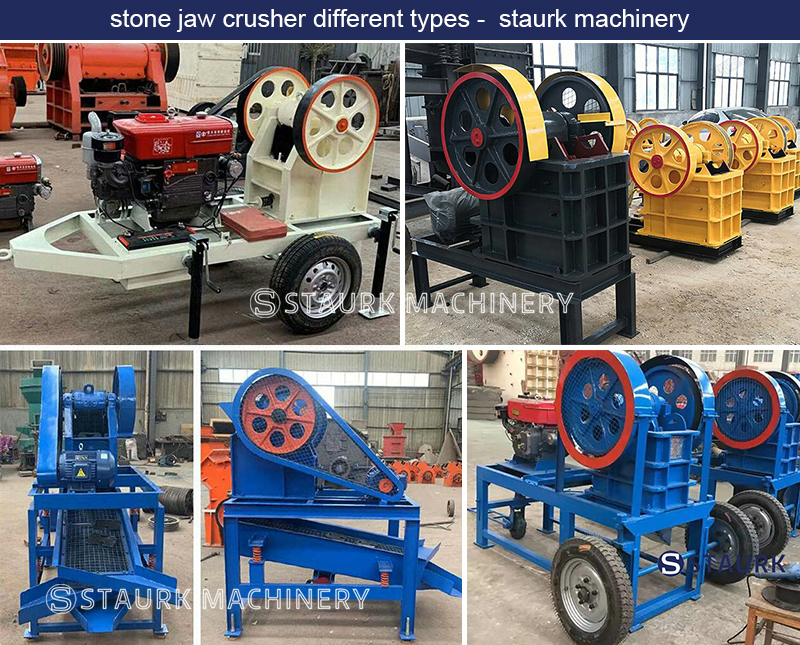
small mobile stone jaw crusher for sale
Fisrt let us see its structure:
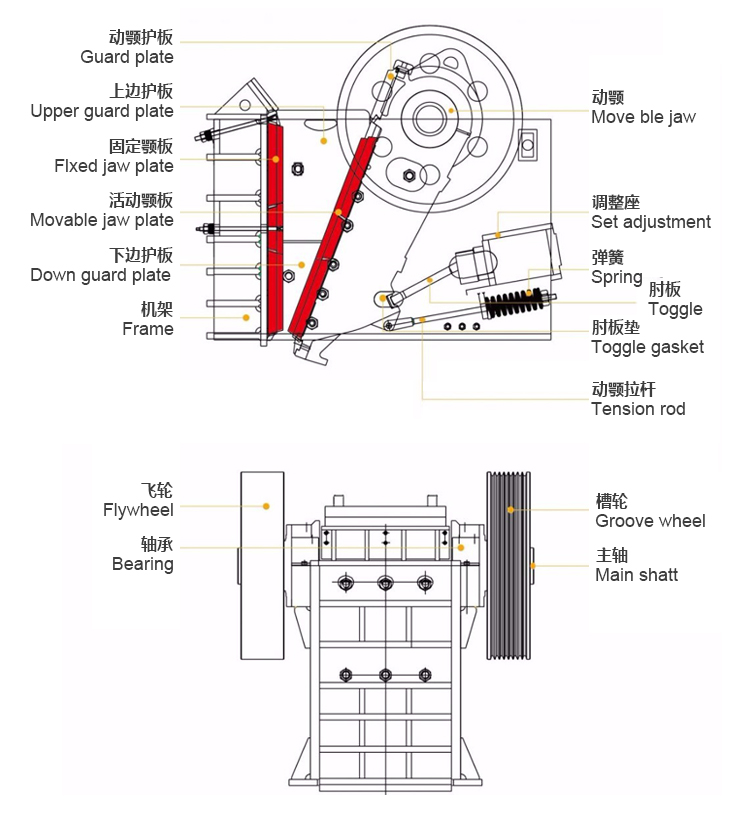
No 1.How to install the jaw crusher?
1.How to install the jaw crusher?
2.how to opreate the jaw crusher?
3.how to repair and examine the jaw crusher?
Related: jaw crusher introduction , parameter,working princeple
Download: jaw crusher operation manual.pdf
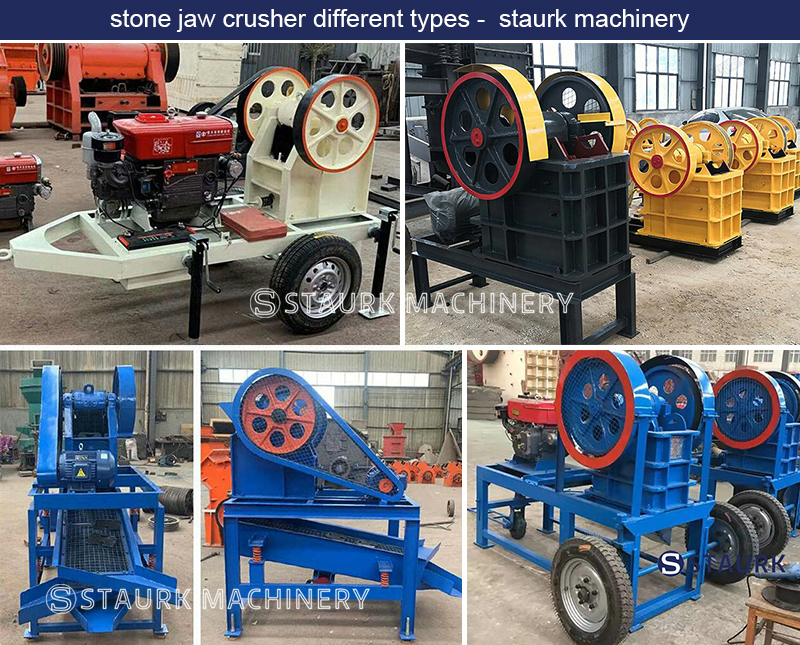
small mobile stone jaw crusher for sale
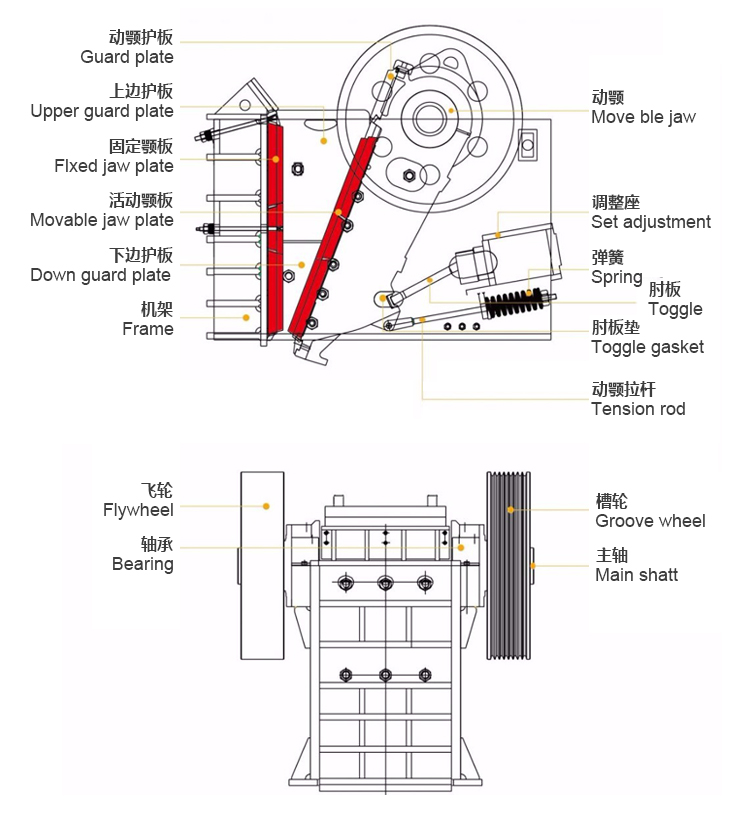
1. Preparation of jaw crush foundation
Jaw crushers are usually installed on concrete foundations, with a drainage trough reserved for the foundation, preferably with a slope of less than 50 degrees. Due to the large vibration of the crusher, it is necessary to isolate the foundation of the crusher from the foundation of the plant.
2. Rack installation
When installing, place something that can absorb vibration between the rack and the concrete, such as hardwood, rubber, etc. The horizontal and vertical horizontality of the rack installed on the foundation or on the wooden base needs to meet the installation requirements of the equipment, generally Should be less than 0.2mm.
3. The main points of assembly of eccentric shaft and bearing
Before assembling the shaft and the bearing, the sliding bearing needs to be researched and assembled, and then placed in the sliding bearing seat, and the level and coaxiality of its placement are tested by using a level gauge. If the measurement results meet the requirements, Then install the eccentric shaft on the bearing, and check the fit between the shaft and the bearing by applying red lead powder on the journal. If there are too many high points on the surface of the sliding bearing, further scraping is required until the high points between the contact surfaces disappear. Finally, apply a certain amount of lubricating oil between the bearing seat and the bearing to reduce the wear of the shaft. The contact area between the eccentric shaft and the frame should not be less than 80%, and the gap between them should be less than 0.07mm.
4. Installation points of the movable jaw
Assemble the movable jaw parts in advance. After assembling the movable jaw, movable jaw shaft, movable jaw plate, toggle pad, etc. on the ground, use a crane or crane to hoist the assembled parts together on the crusher. In the rack. For sliding bearings, it is necessary to grind and match between the bearing and the bearing seat, so as to install the sliding bearing in place. At the same time, check the coaxiality and inclination of the sliding bearing assembly. The inclination should be 0.2mm and the coaxiality should be Less than 0.06mm to complete the assembly of the movable jaw.
5. The installation points of the tooth plate
The tooth plate of the jaw crusher is a part of the crusher directly used for crushing ore. Its structure is simple, but it needs to be replaced frequently due to frequent contact with the ore. The cross-sectional structure of the tooth plate has two types: smooth surface and lattice surface. Due to its heavy weight, it needs to be made into a structure that is easy to replace. The tooth plate is fixed by bolts or wedges, and it is fixed on the front wall of the frame or On the movable jaw, and the contact surface between the two must be straight. If there is a high point in contact, it needs to be dealt with in time. In addition, some aluminum plates can be used for lining between the back of the fixed jaw tooth plate and the front wall of the frame to ensure the tightness of the combination.
No 2.how to opreate the jaw crusher?
1. Preparations before starting: Before starting, a comprehensive inspection of the equipment must be carried out. Check the wear of the crushing gear plate; adjust the size of the discharge port; check whether there is ore in the crushing chamber, if there is a large ore, it must be taken out; check whether the connecting bolts are loose, the protective cover of the belt pulley and the flywheel is intact, the triangle belt and the Whether the tension of the tie rod spring is appropriate, the oil storage tank (or dry oil reservoir) is filled with oil, the lubrication system is in good condition, the electrical equipment and the signal system are normal, etc.
2. Before starting the jaw crusher, you should first start the oil pump motor and cooling system. After 3-4 minutes, when the oil pressure and oil flow indicator are normal, start the motor. After starting, if the jaw crusher makes an abnormal sound, stop the operation, find out and eliminate the defects, and restart the machine. The jaw crusher must be started with no load. After a period of time after the start, the feeder can be started in normal operation.
3. During the operation, attention must be paid to evenly feeding the ore, avoiding lateral feeding or full feeding, so as to avoid unilateral overload or overload. The ore is not allowed to fill the crushing cavity, and the maximum size of the ore block should not be greater than 0.85 times the width of the ore port. At the same time, strictly prevent non-crushed materials from entering the jaw crusher when feeding the mine. During the operation, always pay attention to the large ore getting stuck in the ore port. If it is stuck, use the iron hook to turn the ore; if the large ore needs to be taken out of the crushing cavity, special tools should be used, and hands are strictly prohibited. Do these tasks to avoid accidents.
4. During the operation of the machine, if the ore is fed too much or the crushing cavity is blocked, the ore feeding should be suspended, and the ore in the crushing cavity shall be crushed before starting. During operation, regular inspections should also be made to observe the working conditions of various components and bearing temperature. For large jaw crushers, the sliding bearing temperature usually does not exceed 60°C to prevent the melting of alloy bushes and cause bush burning accidents. When the bearing temperature is found to be very high, effective measures should be taken to reduce the bearing temperature in time (such as forced ventilation or water cooling, etc.).
5. Pay attention to the timely lubrication of the equipment during operation. The grease added to the bearing seat is about 50% of the space volume, and it is replaced every 3-6 months. Clean gasoline or kerosene should be used to clean the raceways of the ball bearings when changing the oil. A proper amount of grease should be injected between the bracket and the bracket seat. When the oil pump suddenly fails, the crusher needs 15-20 minutes to stop due to the large swinging force. At this time, the oil pump must be manually pressed to keep the bearing lubricated and the bearing will not be burnt.
6. In order to ensure the normal operation of the machine, personnel who are not familiar with the operating procedures are not allowed to operate the jaw crusher alone. The machine operators must also receive safety technical education before they can operate.
7. When parking, it must be stopped in the order of the production process. Stop feeding the ore first, and then stop the jaw crusher and belt conveyor after all the ore in the crushing cavity is discharged. When the crusher is stopped, the lubrication and cooling system can be stopped. In winter, the circulating cooling water in the bearing should be discharged to avoid freezing and cracking of the bearing. After shutdown, clean up and inspect all parts of the machine.
8. If the jaw crusher stops suddenly for some reason, the backlog of ore in the crushing cavity must be cleared before the accident is handled and the machine is ready to start operation.
No 3.how to repair and examine the jaw crusher?
#01 Foundation treatment
Jaw crusher is used to crush hard and large raw materials. It is normal to have strong vibration during work, and it is stable with reinforced concrete structure. After running, if there are signs of cracks and looseness, make adjustments to avoid adverse effects on safe operation. In a construction site, due to the impact of the earthquake, the foundation sinks. The downstream side of the jaw crusher frame sinks 35mm more than the upstream side. During the operation of the jaw crusher, the body tilts to the downstream side, and finally the movable jaw frame wears downstream. Side frame, and the upstream side of the main shaft is severely worn, and the internal and external bearings are damaged. The sinking frame needs to be treated in time to ensure the normal production of the jaw crusher.
First, loosen all the anchor bolts on both sides of the frame, and then use two 50-ton jacks to lift about 40mm on both sides of the downstream frame. Then, gouge the bottom of the side, and then according to each bolt Put the cut 30mm steel plate into the lower part. Finally, use high-grade concrete mortar to wipe the surface and ensure that the bolts are tightened after 48 hours of hardening to resume production operations.
#02 Replacing the bottom plate of the feeder
Long-term impact and abrasion with stones caused large cavities in the feed bottom plate of the jaw crusher, and repair welding was no longer possible. After manual cutting, it was found that the original 20mm thick wear-resistant manganese steel plate had been worn out. The iron sheet is full of holes. In this way, the bottom leakage is more serious, which greatly increases the labor of the slag cleaning workers, and the splashing of rocks from the bottom increases the risk of unsafety. Must be replaced to ensure safe production.
First of all, measure the width and length of the bottom plate, and cut off 3 to 5 pieces (to prevent one piece from being too heavy to be lifted to the specified position by mechanical and manual) and other sizes of 20mm thick manganese steel. At the same time, clean up the residue on the bottom plate (to ensure welding Firmly), then, professional welders will fix and weld each steel plate. The welding thickness between the steel plate and the steel plate will be leveled with an angle grinder. After the welding is completed, the weld seam will be inspected to prevent large local wear of the steel plate due to welding defects . After the welding repair is completed, re-install and resume production operations.
#03 Anchor bolt fracture repair
A large number of stones are trapped in the crushing cavity of the jaw crusher due to the over-diameter stone, which causes the crusher to stop. When restarting, the anchor bolts are subjected to a large shearing force, which causes the bolts to be broken under shearing stress; or jaw crushing Machine load vibration, unstable foundation, bearing damage, loose bolts caused by increased eccentric load, swinging of the whole crushing frame, in addition, untimely maintenance and inspection, long-term "illness" work of the equipment, failure to discover in time, and ultimately lead to bolt fracture .
If the anchor bolts are broken frequently, the foundation has cracks, and the cracks are large, there are more hidden dangers in continued use, and the machine must be shut down immediately. The original concrete foundation is removed, the anchor bolts are replaced, and the foundation is re-poured. Remove the original anchor bolt concrete foundation, take out all the bolts, and clean up the working surface; after aligning the machine base, replace all the anchor bolts; grouting the anchor bolt foundation, install the machine after the concrete reaches the strength, and tighten the anchor bolts. After the recheck is correct, proceed to the next procedure; when anchoring movable anchor bolts are used, appropriate reserved pipes should be buried. The grouting generally uses fine gravel concrete.
#04 Spindle repair
As mentioned above, the long-term subsidence of the foundation resulted in serious wear of the spindle on the upstream side. After removing the bearing on this side and lifting and dismantling the jaw, the measurement found that the shaft diameter at this end was 6-12mm smaller than that on the downstream side (due to the lack of wear and tear). Even, the shaft diameter is not a perfect circle), resulting in multiple replacement of the bearing, and the fault cannot be eliminated. Need to deal with the spindle.
Adopt the outer circle surfacing method, and use manual arc welding to evenly surfacing one layer on the worn bearing joint surface. During surfacing, it is advisable to adopt the “small current, small bead, discontinuous” surfacing method, that is, welding a certain length in the red bead. In the state, use a hammer to quickly strike the weld bead, reduce shrinkage stress, water with welding, fast cooling, and improve abrasion resistance. Then re-enlarge the hole according to the requirements of the fit tolerance to achieve the purpose of reasonable matching with the outer diameter of the bearing. This method has a thinner welding layer on the shaft, so there is generally no deformation during surfacing, and there is no special requirement for the welding process. However, the perpendicularity between the center line of the shaft and the two end faces should be controlled when the shaft is processed. To ensure the matching relationship and matching accuracy with other parts.
For emergency repairs at the construction site, you can choose a skilled electric welder to weld 24 vertical seams evenly on the bearing. After the height is polished, the height is 5mm higher than the original shaft, and then touch some white ash on the 24 vertical seams, and sleeve the bearing. Where there are no traces of white and gray on the inner sleeve of the bearing, it can be assembled and used until it is in good fit with the inner sleeve (ensure that the shaft is a perfect circle).
#05 Replacement and lubrication of the inner and outer bearings of the movable jaw
During the operation of the jaw crusher, a piercing noise occurred, and the jaw crusher was stuck in a short period of time, and the flywheel no longer rotated. Disassemble the flywheel and open the protective cover. It was found that the outer bearing cage of the movable jaw was damaged, and the inner rolling balls were scattered and damaged; after the movable jaw was lowered, it was found that the internal bearing was also partially damaged.
First, deal with the bearing of the movable jaw: boil the stock spare bearing for 2 hours, and use a sledgehammer pad copper rod to hammer in turns to wedge the bearing into its original position. After that, the whole movable jaw is hoisted. For external bearings, the main shaft can be lifted by the self-made steel pipe pad jack, and the bearing can be lifted onto the shaft by a small crane, and then hammered into the specified position according to the steps. Then hoist the flywheel, install the V-belt, and start the machine after debugging. The grease used in the jaw crusher should be determined according to the place of use and temperature conditions. Generally, calcium-based, sodium-based and calcium-sodium-based greases are used. The grease added into the bearing housing is about 50% of its space volume and replaced every 3 to 6 months. Clean gasoline or kerosene should be used to clean the raceways of the roller bearings when changing the oil.
#06 Toggle replacement
During the production process, the brackets are often subjected to cracks and even cracks due to large forces. What's more, there will be transverse faults, which need to be replaced in time. When replacing, first take out 2 to 3 pieces of steel plate that is used to adjust the size of the feed opening, push the jack forward to prevent the movable jaw from falling, hang the bottom of the movable jaw with a wire rope and connect it to the machine with a 5 ton inverted chain on the upper part. Tension on the frame and loosen the adjusting rod bolts. At this time, you can use steel drills on both sides at the same time, cooperate with the crane to slowly lift out the waste brackets, and then install the new brackets and tighten them everywhere to use.
#07 Bracket crack treatment
When replacing the bracket, it was found that there were cracks in the channel steel clamped by the bracket seat, which eventually caused the bracket to move in the seat, thereby reducing the service life of the bracket. Need to deal with the bracket seat. Taking out the channel steel in the clamp is the focus of this work.
First, take out the channel steel plan by bolt fastening, that is: weld and fasten high-strength bolts at both ends of the channel steel and 3 places in the middle, and cut three steel plates with bolt-sized holes in the middle, and fasten them at the same time through three wires. Attempt to take out the channel steel, but because the channel steel has been bitten to the bracket seat, although the method broke a few bolts and bent the steel plate, the channel steel was not taken out.
After that, oxygen acetylene is used to cut the cracks from the middle of the channel steel, and then the two channels are taken out respectively, and finally the channel steel is taken out, and the new channel steel is embedded and welded to the bracket seat, and then installed and used.
#08 Reverse and replace the jaw
After a period of normal wear and tear of the jaws, the facial racks will be dull or completely flattened. The upper and lower jaws need to be reversed for multiple use. After the second grind, you need to replace the new jaw.
First, the bolts of the wedge, guard plate and slide plate need to be removed and lifted out in sequence, and then the lifting lugs are welded on the upper part of the jaw to be lifted out. Re-weld and fix the lifting lugs and install them at the bottom (not needed if renewed). The second jaw is also installed backwards. To install the jaw plate of the assembled jaw crusher, it needs to be firmly attached to the jaw bed, and soft metal is used as a gasket to ensure that it is leveled and then tightened with bolts before use. During the working process of the crusher, regularly check whether the jaw plate is loose. If it is loose, even adjust it to prevent it from breaking or abrasion, so as to reduce the service life of the jaw plate.
#09 Handling over-diameter materials
Because the raw materials are mountain blasting stones, and the Komatsu PC360 excavator is used for loading and Steyr dump trucks are used for transportation, it is inevitable that there will be over-diameter materials, which will affect the production efficiency of the coarse crusher. After the super-diameter stone enters the feed port of the coarse crusher, it will block the feed port, affecting normal operation, and the processing is time-consuming and unsafe. The system has had safety accidents due to the processing of super-diameter materials. Therefore, the super-diameter material in the wool must be processed before entering the feed port of the coarse crusher of the sand production line.
To deal with over-diameter materials, we adopt the pre-screening method, blasting method, crushing hammer crushing method, and squeegee lifting method for processing. The grid bar screen pre-screening method uses a 43kg/m steel rail to make a grid bar screen with a sieve hole of 400×400mm. In use. The rail is constantly impacted by the stone material, and the deformation is large, and the removed super-diameter material is not easy to be transported away. The blasting method on the screen surface also takes labor and time and affects the normal feeding of the coarse crusher; the blasting method and the hammer crushing method can only process the super-diameter stone on the surface of the pile. However, the super-diameter stones inside the stockpile cannot be processed, and the problem cannot be solved fundamentally; the lifting method of the mast (crane) adopts a mast (or erection of a crane) and a single drum hoist (or crane) on the side of each coarse crusher silo. When lifting, the lifting weight is not less than 5 tons. The super-diameter stones that have entered the silo are tied up with steel ropes and then hoisted out, the guns are concentrated, and then the loader is used to feed the silo.
#10 Handle the feeder pulley sliding key
The spline between the feeder belt pulley and the shaft has a feather key phenomenon after long-term operation. We adopt roller extrusion or surfacing to reprocess it to the basic size. Manual arc welding is generally not recommended because it has a great impact on the material of the parts. Or reduce the keyway by electric welding and use an angle grinder to polish the processing method, or re-process the keyway on the pulley using a new spline fit method. The surfacing layer is uniform and tight, without block loss, delamination, slagging, and no cracks, burns, etc.; if the matching backlash between the spline tooth and the sleeve is less than 3% to 4% of the tooth width, it is not allowed to be repaired , The use limit is 10%. For the small value of fixed combination, the positive and negative ones can be larger. At the same time, external bolts are used to tighten the steel plate during installation to prevent the spline and the pulley from shaking left and right.