Rod Mill operation manual : how to install use maintain it
2022-11-13
staurk machinery
As a rod mill manufacturer , we will introduce its operation manual:
1.how to install rod mill
2.rod mill test run
3.how to opreate rod mill
4.maintenance of rod mill
5.how to replace the roller skin
Related product introduction:
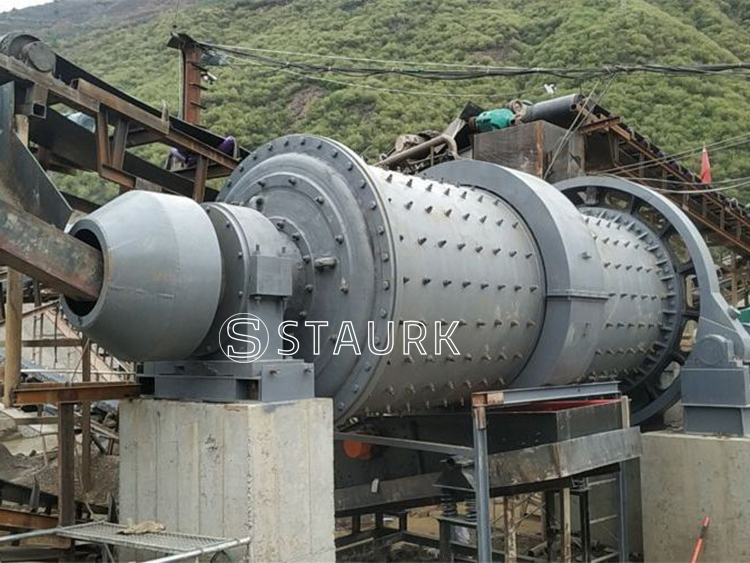
1.how to install rod mill?
The rod mill should be installed on a solid concrete foundation.
The rod mill can be installed on the concrete foundation after the compressive strength reaches more than 75%.
The quality of the foundation should be inspected before installation. It is required that the concrete has no defects affecting the strength, the number and position of the reserved holes meet the requirements, and there is no sundries, accumulated water and oil in the reserved holes.
Before installation, draw all punch marks on the basis as the centerline reference during installation.
Before hoisting, the sub-parts of the rod mill should be fully checked and accepted, and problems should be dealt with in time.
General requirements for rod mill installation:
1.1. Installation of the host:
The axis of the main machine of the mill should be horizontal, measured at the top of the large flange of the hollow shaft at both ends, the height should be consistent, and the feed end is allowed to be 1mm higher than the discharge end when there is an error. Look, the gap between the hollow shaft and the bearing gland should be basically the same, and the gap at the inner and outer glands should be basically the same.
1.2. Installation of the transmission part:
The installation of the transmission part can only be carried out after the main engine is adjusted to the level.
Based on the large gear of the main engine, install and adjust the transmission part. Make the tooth width of the pinion gear ratio uniform on both sides of the tooth surface of the large gear. Make the tooth surface of the pinion gear parallel to the tooth surface of the large gear, and leave the backlash of 0.25mm at the minimum. From the contact traces of the big and small gears, the contact traces should account for more than 60% of the total length, and the height of the contact traces should account for about 40% of the total height.
If the contact marks are offset to one end of the flank width, it means that the flanks are not parallel. If the large gear is squeezed all around, it means that the gear gap is too small, and the pinion should be kept away from the large gear.
1.3. Installation of mill liner:
(1) Before installing the liner, the dirt in the cylinder should be cleaned first. The bolt hole should be thoroughly cleaned of sand and casting flash, so that the bolt can penetrate smoothly.
(2) When installing the lining plate, a layer of 1:2 cement mortar should be applied between the inner wall of the cylinder and the lining plate, and the bolts of the lining plate should be tightened while wet. The gaps between the liners are also smoothed with mortar.
(3) The bolts for fixing the lining plate should be carefully cushioned to prevent the leakage of ore pulp or ore powder.
(4) The cylinder liner shall not form an annular gap.
(5) After the cement mortar has solidified to meet the strength requirements, it can be put into trial operation. If the bolts are found to be loose during operation, they should be tightened in time.
2. Test run / Trial operation of rod mill
(1) The continuous operation time of idling is not less than 12-24 hours, and problems found during operation should be solved in time.
(2) The load test run can be carried out when the dry running test machine is normal. The load test run shall be carried out in stages. During the load operation, feeding should be carried out according to the discharge situation to avoid unnecessary wear and damage of the steel rod and the cylinder liner.
1. Add appropriate materials and 1/3 of the number of steel bars, and run for 12-24 hours.
2. Add to 2/3 of the number of steel bars and run for 24-48 hours.
3. According to the discharge situation (qualified products) and output of the rod mill, the reasonable rod loading capacity of this rod mill should be determined with reference to the actual rod loading capacity of the same type of rod mill in the same industry, and carry out a period of not less than 72 hours. Test run.
(3) The increase of the above load and the length of the test run time are determined on the basis of the running-in conditions (temperature rise, noise, tooth surface contact, etc.) of the large and small gears and the gears of the reducer. Do not operate at full load until the contact accuracy of the tooth surface does not meet the design requirements.
(4) The cooling and lubrication system should work normally during the test run. The temperature of main bearing, transmission bearing and reducer should be normal.
(5) After 24-48 hours of trial operation with 2/3 of the steel bars, check and re-tighten all the bolts.
(6) Various records should be carefully made in the trial operation work.
3. Operation of rod mill
(1) Preparations before starting:
1. Check whether there is anyone in the dangerous place.
2. Check whether the lubricating oil level of each lubricating point is appropriate, and add it if it is insufficient.
3. Check whether the filling rate of steel rods in the rod mill meets the requirements.
4. Check whether the bolts of the grinding body lining plate, the connecting bolts of the grinding head and the cylinder body are loose and tightened reliably.
5. Fix the manhole cover reliably and tightly.
6. Check whether there is water leakage or powder leakage in the bolt holes and manholes of the cylinder and eliminate them.
7. After the first test run or long-term stop grinding, when starting again, first pour a small amount of lubricating oil on the hollow bearings at both ends, and use manual disc grinding for one week, or "jog" for one week to confirm that there is no abnormal phenomenon.
8. Get in touch with the relevant jobs before and after, and start the mill only after getting the signal to allow the start.
(2) The sequence of startup:
1. Start the rod mill.
2. Start the feeder.
(3) The sequence of shutdown:
1. Stop the feeder.
2. Stop the rod mill. Long-term stop grinding should unload steel rods and materials.
4.Maintenance and overhaul of rod mill
1. All lubricating oil should be released when the mill is put into continuous operation for one month, thoroughly cleaned and replaced with new oil. In the future, combined with the revision, the oil will be changed every 6 months.
2. Check the lubrication condition and oil level of each lubrication point at least every 4 hours.
3. When the mill is running, the temperature rise of the main bearing lubricating oil should not exceed 55℃.
4. When the mill is in normal operation, the temperature rise of the transmission bearing and reducer should not exceed 55℃, and the maximum temperature should not exceed 60℃.
5. The large and small gears drive smoothly without abnormal noise. The gap should be adjusted in time if necessary.
6. The rod mill runs smoothly without strong vibration.
7. There should be no abnormal fluctuations in the motor current.
8. There is no loosening of the connecting fasteners, and there is no oil leakage, no leakage of slurry, and no leakage of powder on the joint surface.
9. Steel rods are added in time according to wear conditions.
10. If abnormal conditions are found, the grinding should be stopped immediately for maintenance.
The maintenance of the mill is a regular work, and the quality of the maintenance work directly affects the operation rate and service life of the rod mill. In order to find defects in time and eliminate hidden dangers, so as to ensure the normal operation of the rod mill, in addition to daily maintenance, it is also necessary to stop grinding regularly (it is recommended to once a month). Gears, etc. shall be carefully checked and detailed records shall be made. Appropriately handle and arrange intermediate and major repair plans according to the priority of the defects.
11. The lining plate of the mill should be replaced when it is worn by 70% or has 70mm long cracks.
12. If the lining bolts are damaged and the lining is loose, it should be replaced.
13. The main bearing should be replaced when it is seriously worn.
14. The grate plate should be replaced when it is worn to the point where it cannot be repaired by welding.
15. After the gear surface of the large gear is worn to a certain extent, it can be turned over and continued to be used.
16. The pinion gear should be replaced if it is seriously worn.
17. When the feeding and discharging spirals are worn, they should be repaired by welding in time, and they should be replaced when they are worn to the point where they cannot be repaired by welding.
18. Loose or damaged anchor bolts should be repaired in time.