In-depth knowledge of gravity separation process plant & machine
2021-07-14
Staurk Machinery
Guide line:
1.Definition of gravity methord
2.Application of gravity
3.Advantages of gravity
4.Disadvantages of gravity
4.Disadvantages of gravity
5.Notes of gravity
6.Classification of gravity
6.Classification of gravity
7.Gravity machines
Details:
2.Application of gravityDetails:
1.Definition of gravity methord
Gravity separation is a method of sorting according to the different mineral specific gravity and the different settlement velocity in the medium(mainly is water).
In the process of re separation, the ore particles with different specific gravity are sorted in the moving medium because of their different motion state, velocity, direction and way.
The results show that the larger the particle size and the specific gravity of ore particles, the larger the settlement velocity in a certain medium. If the particle size is the same, the final velocity of the deposit is larger than that of the major one.
In the process of re selection, there are water, air, heavy liquid and suspension used as the separation medium. Heavy liquid is a liquid with a specific gravity greater than water. Suspension is a two-phase liquid composed of water and solid particles suspended in it.
The main applications are as follows
① Separation of gold, platinum and other precious metals;
② Separation of tungsten and tin ores;
③ Processing of placers containing rare metal elements, such as the separation of coastal placers containing zirconium and titanium minerals;
④ Separation of hematite and limonite;
⑤ Separation of manganese ore;
⑥ Separation of coal and gangue in coal preparation plant;
⑦ Separation of some nonmetallic minerals from gangue, such as asbestos, mica, kaolin, sepiolite and diamond;
⑧ For those nonferrous metal ores, such as copper, lead and zinc, which are mainly treated by flotation, gravity separation is used for preconcentration;
⑨ The process of particle size separation in gravity separation, such as classification, desliming, etc.
3.Advantages of gravity
The separation efficiency is often low when dealing with fine-grained materials,Gravity separation has a wide range of particle size, which is especially suitable for coarse-grained materials with a certain specific gravity difference.3.Advantages of gravity
① Compared with other methods, gravity separation method is simple and low cost. Therefore, it is an indispensable operation in almost all concentrators.
② Gravity separation is suitable for a wide range of particle size, from several hundred mm to less than one mm, with low cost and less environmental pollution.
4.Disadvantages of gravity
4.Disadvantages of gravity
5.Notes of gravity
In order to separate the ore particles according to the specific gravity as much as possible, the ore must be fully broken(by jaw crusher ,hammer crusher , ball mill ,wet pan mill etc.) before gravity separation, so that the useful minerals in the ore can reach monomer dissociation and reduce the maximum block size into gravity separation. Screening and classification is to divide the ore particles into various sizes for different gravity separation operations.
6.Classification of gravity beneficiation methods
Gravity separation method can be divided into hydraulic or wind classification, ore washing, heavy medium beneficiation, jigging beneficiation, chute beneficiation and shaker beneficiation.
7.Gravity machines
1)Jigging beneficiation
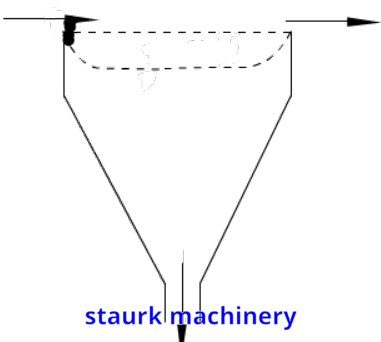
1.Jigging beneficiation by jigger machine, is one of the main methods of gravity beneficiation, which belongs to deep tank beneficiation.
2.Jigging beneficiation, in addition to very fine materials, can handle almost all kinds of particle size of mineral raw materials
3.The process operation is simple, the equipment processing capacity is large, and a final product can be obtained in one separation
4.For metal ore, it is the main method to treat coarse and medium grained iron ore, manganese ore and chromium ore.
5.It is also widely used to separate the coarse-grained parts of tungsten and tin ores with uneven distribution.
6.Jigging machine is widely used in the treatment of gold bearing placer, primary ore and placer containing niobium, tantalum, titanium and zirconium. It is also the main method for diamond separation.
7.The larger the density difference of minerals to be separated, the wider the range of particle size.
8.For example, for placer gold ore, when the feed particle size is less than 25 mm, it can be selected without classification, and the lower limit of recovery particle size can be 0.04 mm. However, for general metal ores, classification can effectively improve the separation index and equipment processing capacity.
9.On the premise that the specific gravity difference is greater than or equal to 1.25 and the ore monomer is dissociated, the grain size of the jigging machine is 150 ~ 2mm, the grain size range of other minerals is 50 ~ 0.1mm, and the lower limit grain size of placer gold can reach 0.04mm.
2)Shaker beneficiation
The shaker by shaking table is a common equipment for separating fine ore, and the effective separation size range of metal ore is 3 ~ 0.019mm,
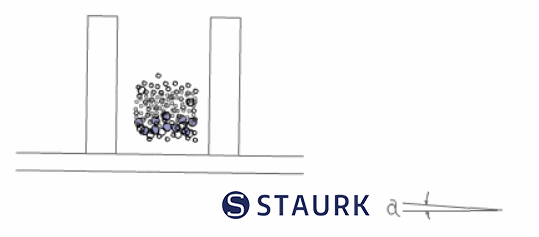
The outstanding advantage of the shaking table is high separation accuracy. High grade concentrate or waste tailings can be obtained after one separation, and multiple products can be obtained at the same time.
The finer the particle size, the smaller the processing capacity.
3)Sluice concentration
Chute beneficiation belongs to inclined flow separation process. When the slurry is fed to a certain inclined chute or inclined plane, the ore particles are loose and layered under the push of water flow, and the fine minerals in the upper layer are quickly discharged out of the chute, while the heavy minerals in the lower layer are retained in the chute or discharged from the lower part at a low speed. The concentrate and tailing can be obtained after being taken separately.
Chute is the earliest mineral processing equipment.
At present, belt chute is widely used to treat low-grade fine-grained (- 0.074mm) placer of rare metal ores such as tungsten, tin, gold and platinum
4)Spiral dressing
Spiral beneficiation is a beneficiation process which is carried out in a long curved spiral trough. It still belongs to the category of inclined flow beneficiation. However, the inertial centrifugal force produced by the slurry in the rotary motion is used here to promote the fine and heavy minerals to be separated on the trough surface and discharged continuously.
Spiral chute
The flow and separation principle of pulp in spiral chute are basically the same as those of spiral concentrator. But the spiral chute has a larger flat width on the surface, and the area of slurry laminar flow is larger, so it is suitable for the treatment of fine-grained ore.
Spiral chute also has the advantages of simple structure, large processing capacity, convenient operation and low production cost. It is suitable for processing 0.6 ~ 0.03mm vein ore or placer ore, but it is unfavorable for separation when the mud content is high. The enrichment ratio of mineral processing is also low.
5)Centrifugal beneficiation
Centrifugal separation is mainly by means of centrifugal force, which speeds up the sedimentation and stratification speed of fine particles, and is suitable for the treatment of-0.1 mm fine particles. Because the production cost is relatively high compared with the general gravity selection method, and the recovery effect of 37 ~ 19 micro meter is very good.
At present, it is mainly used to deal with high value micro materials such as tungsten.
At present, it is mainly used to deal with high value micro materials such as tungsten.
Compared with the shaking table, in the treatment of 0.037 ~ 0.019mm materials, the centrifugal concentrator has the advantages of less floor area, large processing capacity, saving power consumption, etc., but its concentration ratio is low, and its concentrate needs to be cleaned by belt chute to reach the final concentrate.
6)Wind power beneficiation
Wind power beneficiation is a process of separating mineral raw materials according to mineral density difference in air medium. The particle size and shape also affect the separation.
Due to the relatively complex process and low beneficiation efficiency, its application has great limitations. At present, it is mainly used for processing coal, asbestos and other non-metallic ores, especially for processing mineral raw materials which are not suitable for water.